自動(dòng)焊接設(shè)備注意事項(xiàng)以及分類
來源:http://m.tj-moju.com/ 發(fā)布時(shí)間:2021-03-08 瀏覽次數(shù):0
自動(dòng)焊在當(dāng)下的適用范圍非常的廣,自動(dòng)焊受歡迎的原因在于自動(dòng)焊相比較傳統(tǒng)焊接方法來看,焊接精度更加準(zhǔn)確,而且隨著近幾年自動(dòng)焊的應(yīng)用,越來越多的人開始關(guān)注自動(dòng)焊的發(fā)展,下面,就讓我們一起來深入了解一下自動(dòng)焊接設(shè)備的注意事項(xiàng)以及分類吧。
Automatic welding has a wide range of applications at present. The reason why automatic welding is popular is that compared with traditional welding methods, automatic welding has more accurate welding accuracy. Moreover, with the application of automatic welding in recent years, more and more people begin to pay attention to the development of automatic welding. Now, let's have a deep understanding of the precautions and classification of automatic welding equipment.
山東自動(dòng)焊接設(shè)備
Shandong automatic welding equipment
自動(dòng)焊接設(shè)備的注意事項(xiàng):
Precautions for automatic welding equipment:
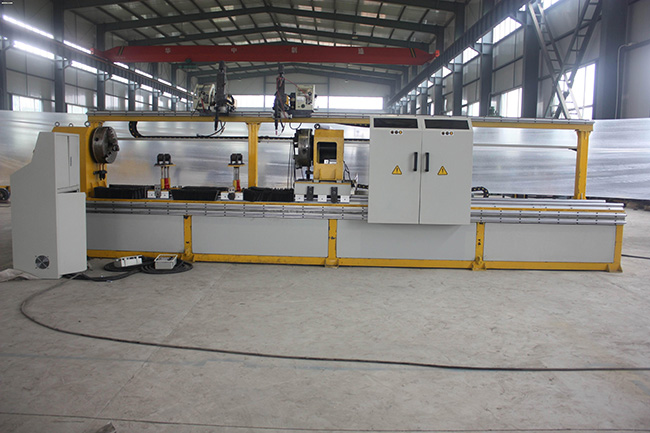
1、靈活多樣的焊接方法同時(shí)支持點(diǎn)焊和電阻焊接(拉焊)。自動(dòng)焊設(shè)備的所有工藝參數(shù)可由客戶自行設(shè)定,以適應(yīng)各種困難的焊接操作和微焊接工藝。所有焊接參數(shù)可隨焊點(diǎn)坐標(biāo)程序一起讀取和保存,從而完成焊接操作的靈活性。
1. Flexible welding methods support spot welding and resistance welding (pull welding). All process parameters of automatic welding equipment can be set by customers to adapt to all kinds of difficult welding operation and micro welding process. All welding parameters can be read and saved together with the solder joint coordinate program, so as to complete the flexibility of welding operation.
2、烙鐵組件可以任意角度和方向調(diào)節(jié),控制烙鐵組件的R軸,360度自由旋轉(zhuǎn)。焊接次數(shù)、預(yù)熱時(shí)間和焊接時(shí)間可以根據(jù)不同的焊盤和元器件任意設(shè)定,從而完成一個(gè)板上多個(gè)焊點(diǎn)的復(fù)雜焊接過程,焊接操作多樣化。
2. The soldering iron assembly can be adjusted in any angle and direction to control the R-axis of the soldering iron assembly and rotate 360 degrees freely. The welding times, preheating time and welding time can be set arbitrarily according to different pads and components, so as to complete the complex welding process of multiple solder joints on a board, and the welding operation is diversified.
3、四軸/五軸聯(lián)動(dòng)機(jī)械手和自動(dòng)焊設(shè)備均采用伺服驅(qū)動(dòng)和的運(yùn)動(dòng)控制算法,有效提高了移動(dòng)端焊頭的定位精度和重復(fù)精度,完成了三維空間任意焊點(diǎn)的準(zhǔn)確定位。
3. Four axis / five axis linkage manipulator and automatic welding equipment adopt servo drive and advanced motion control algorithm, which effectively improves the positioning accuracy and repetition accuracy of the mobile end welding head, and completes the accurate positioning of any solder joint in three-dimensional space.
根據(jù)程度,自動(dòng)焊接設(shè)備可分為以下三類:
According to the activation degree, automatic welding equipment can be divided into the following three categories:
1。剛性自動(dòng)焊設(shè)備:剛性自動(dòng)焊設(shè)備也可稱為初級自動(dòng)焊設(shè)備,大多數(shù)都是根據(jù)開環(huán)控制原理設(shè)計(jì)的。雖然整個(gè)焊接過程都是由焊接設(shè)備主動(dòng)完成的,但閉環(huán)反饋系統(tǒng)不能應(yīng)用于焊接過程中焊接參數(shù)的波動(dòng),可能出現(xiàn)的偏差也不能隨意修正。
1。 Rigid automatic welding equipment: rigid automatic welding equipment can also be called primary automatic welding equipment, most of which are designed according to the open-loop control principle. Although the whole welding process is actively completed by the welding equipment, the closed-loop feedback system can not be applied to the fluctuation of welding parameters in the welding process, and the possible deviation can not be arbitrarily corrected.
2、自控式自動(dòng)焊設(shè)備:自控式焊接設(shè)備是一種具有高度主動(dòng)性的焊接設(shè)備。配有傳感器和電子檢測電路,主動(dòng)引導(dǎo)和跟蹤焊接軌跡,并由閉環(huán)對主要焊接參數(shù)進(jìn)行反饋控制,整個(gè)焊接過程將根據(jù)預(yù)設(shè)的程序和工藝參數(shù)主動(dòng)完成。
2. Automatic control welding equipment: automatic control welding equipment is a kind of welding equipment with high initiative. It is equipped with sensors and electronic detection circuit to actively guide and track the welding trajectory, and feedback control the main welding parameters by closed loop. The whole welding process will be completed according to the preset program and process parameters.
3、智能自動(dòng)焊設(shè)備:智能自動(dòng)焊設(shè)備采用視覺傳感器、觸覺傳感器、聽覺傳感器和激光掃描儀等各種傳感元件,依靠計(jì)算機(jī)軟件系統(tǒng)、數(shù)據(jù)庫和系統(tǒng),具有識別、判別、實(shí)時(shí)檢測、操作、主動(dòng)編程、焊接參數(shù)存儲(chǔ)和主動(dòng)生成焊接記錄文件的功能
3. Intelligent automatic welding equipment: the intelligent automatic welding equipment adopts various sensing elements such as visual sensor, tactile sensor, auditory sensor and laser scanner, and relies on computer software system, database and expert system. It has the functions of recognition, discrimination, real-time detection, operation, active programming, welding parameter storage and active generation of welding record file
上一篇:焊接設(shè)備的使用應(yīng)注意以下幾個(gè)方面
下一篇:山東數(shù)控焊接設(shè)備的參數(shù)比較